Case Studies
Top^
Manufacturing innovation that delivers superior results
Stug delivers with a personal service philosophy that understands your requirements for quality, design, price and turnaround time.
Top^
Stug rises to meet a cheesy challenge
Product from previous manufacturer
A cheese manufacturer needed to replace 300 transfer cassettes, used for holding the cheese while its weight was checked. All cassettes needed to have a consistent weight, with a variation of only 20 grams (about the same as a standard post-it note) and also engraved with a unique number, from 1-300.

Improved solution from Stug
A previous supplier had met the weight requirement by manufacturing the cassettes slightly overweight and then drilling holes in them until they weighed the correct amount (see photo). However this gave them an unsightly appearance and created a contamination hazard as the drilled holes were much harder to keep clean. Plus it raised the price of manufacture.
Stug's engineers re-designed the part with encapsulated weights within the plastic base that could be altered to ensure that every cassette was within a tolerance of plus or minus 10 grams, (half the original specification) and created a hygienic component with improved appearance.
Product in situ
Superior Result:
- Efficient manufacture meant that the final price was under the customer's expected budget
- Additional savings were gained because the weights can be replaced and reset at any time, so the parts can be easily repaired and reused if they are damaged
- The parts exceeded the customer's challenging specifications.
Top^
Gearing up for huge cost savings
An entire unit used by a pharmaceutical manufacturer needed to be replaced every time one of the three gears became worn.
Stug reverse engineered the three gears in the unit and then manufactured replacement parts as required. This proved more cost effective than purchasing an entire unit, as well as environmentally responsible by creating less wasted parts.
Superior Result:
- New machined parts stronger than original injection moulded parts
- Wear resistance and part longevity improved by upgrading to a higher grade of material
- Forward orders of your custom parts can be manufactured in advance and kept as stock, saving you time and money when you need replacements.
Top^
High import costs had customer over a barrel
This metal filling barrel used on a food processing line was totally imported and had to be purchased as part of a complete assembly. The centre shaft was plated in hard chrome and had poor durability causing bits to flake off as it became worn and created a contamination problem.
Stug reverse engineered the part and changed the centre shaft coating to a durable black nitride. High-wearing plastic was added into areas where wear was significant. Individual spare parts were manufactured and sold separately, removing the need to buy a whole assembly for just one part.
Superior Result:
Stug improved performance and saved money in three ways:
- The filling barrel was cheaper to purchase because it could be bought individually and locally rather than as part of an imported assembly
- Combining food grade plastic and metal improved wear resistance, reducing costly down time
- Changing to black nitrite plating reduced risk of contamination and improved durability.
Top^
One-stop shop for plastics, metals, plating and assembly
A medical equipment manufacturer required an assembly of high-precision components machined from two different metals (black-anodised aluminum and brass) as well as plastic (acetal).
Most machining companies have high-precision expertise in plastics or metals, but not both. Not all arrange for coating or plating of parts.
When parts are purchased from different suppliers they must be assembled by the client, or by a third supplier, and there is the risk that parts will not fit together well.
Stug's expertise in precision machining of both plastics and metals, as well as our coating and assembly services, meant that one supplier could provide the assembled item, ensuring all parts would fit and work together.
Superior Result:
- Time and money savings by dealing with just one expert supplier
- Confidence that all parts will fit together well, compared to the risk when parts are made and assembled by various suppliers.
Top^
Sprockets that rocket with improved wear and functionality
Idler sprockets used in a food processing line were originally made from a heavy metal and kept wearing out.
Stug replaced the metal with nylon, which is lighter and harder wearing. A bronze bearing added to the centre of each part meant that the bearing only could be replaced rather than having to replace the entire item.
Superior Result:
- Improved wear resistance, reducing costly down time and line stops
- Easy and low cost repairs, saving time and money
- Reduced weight, resulting in power savings and longer machinery life.
Top^
Stug sends problems packing with innovative CAD file solution
A personal hygiene products manufacturer changed to a different shaped container requiring a new feed gear for their processing and packaging line.
Stug reverse engineered their existing imported parts and then designed and manufactured feed gear to suit the new container shape. Using a local supplier makes updating to new containers easy and fast.
The design is stored as a CAD file so ordering of replacement parts is easy, with a quick turnaround, and the assurance of complete repeatability of parts. If another new design is required this can be done very quickly by modifying the existing CAD file.
Superior Result
- Easy and quick to change container shapes, providing greater flexibility and reducing changeover costs
- Quality replacement parts with complete repeatability
- Cost effective compared to imported parts
- Shorter lead time on new container designs and replacement parts when required
- Convenience of a local, Australian-owned expert manufacturer.
Top^
Wine bottles filled with innovation
Screw caps are increasingly replacing corks in the wine industry but a popular brand of wine bottling machine was unable to fill screw capped bottles at normal production speed and filling valves had a high incidence of failure due to fatigue. In response we developed the Stugfilla valve which enables a return to optimal speed and has a significantly reduced failure rate. Stug’s cost-effective solution has solved a major productivity issue for wine bottlers, saving them thousands of dollars.
Superior Result:
- Increased productivity – an improvement of up to 33% when filling screw capped bottles
- Increased reliability – Stugfilla™ valves have performed without failure due to fatigue over a 4 year period under normal production conditions
- Increased versatility – the valves can be used at optimal speeds for filling both corked and screw capped bottles
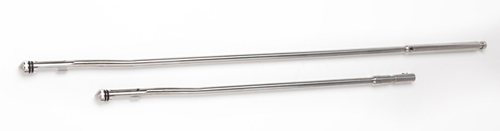
Top^
Light and easy does it for building products company
A building products company needed to replace a chute made from mild steel, which was in a wet and abrasive environment that caused a rust problem. The metal chute had to be removed regularly to be cleaned, and because it was so large and heavy it needed 2 people to lift it.
Stug re-designed the chute using polypropylene, an economical but hard wearing plastic. It was lined with UHMWPE, a high-grade polyethylene with exceptional abrasion resistance and sliding properties.
Superior Result:
- Because polypropylene is lighter than steel the weight of the chute was significantly reduced, meaning it could be lifted by one person, saving time and money in the cleaning process as well as reducing occupational health and safety risks
- Unlike the original steel outer shell, polypropylene has greater corrosion resistance and doesn't rust, increasing durability in this wet and abrasive application and reducing maintenance costs such as painting of the steel chute
- The high quality UHMWPE lining added to the wear resistance of the final product, saving time and money in replacement costs and line stops
- Stug's combination of engineering skills and plastic fabrication produced a high quality product which fitted and worked with other parts on the processing line.
Top^
Customer bottled over with award-winning innovation
A leading pharmaceutical company changed its bottle size but the injection molded bottle holders in their bottle washing machine did not suit the new bottle, so it wasn't being washed effectively and the cost to re-tool was prohibitively high.
Stug worked with the company to redesign the bottle holder shape to suit the new bottles and machined the new bottle holders at a fraction of the cost of re-tooling.
The new machined parts were stronger than injection moulded ones. Plus Stug was able to meet or exceed all the customer's specifications including using a special coolant to meet strict contamination requirements and full batch traceability on the material used.
Superior Result:
- The customer won a national award for efficiency improvement with this project
- A customised product which met the customer's specifications, driven by a commitment to understanding their requirements for quality, design, price and turnaround time
- Flexibility to change bottle design easily and economically.
Top^
Stug provides a sweet solution to a sour material problem
This kettle blade was used by a confectionary manufacturer but it was subjected to high heat and caused hydrolysis in the ertalyte material it had been manufactured from, leading the blade to crack and fragment. This in turn led to contamination of the product, with the associated costs of line stops, constant replacement of the blades and product wastage.
Stug identified the correct material for this application - PPS, a high performance plastic which can withstand temperatures up to 260 degrees Celsius and is FDA approved for food contact. Although this is a more expensive material initially, the savings in improved performance over time outweighed the up-front cost.
Superior Result:
- Less down time with improved performance
- Safely manufactured product
- Significant savings over time.
Top^
Innovation gives brass the flick and saves $$ for food processor
An original brass pick and place gripper part was worn and causing line failure, costing tens of thousands of dollars in down time and damaged or wasted products. Stug's innovative and cost effective solution was to reverse engineer the guide pin within the part with the high performance plastic PEEK HPV to give greater wear resistance.
Superior Result:
- Dramatic reduction in unit cost
- Significant increase in wear resistance
- Lower failure rate & less down time, saving thousands of dollars
- Higher productivity & less frustration for production and maintenance staff
- Time and money savings from choosing a locally made replacement part compared to the cost of importing the part.
For expertise, precision, quality and service we extend an invitation to you to contact Stug Australia for the solutions you require.
Call 03 9543 5044 or fill in the form below for more information.
|